Suppression complète du polissage avec des effets annexes positifs
On appelle ça frapper ou forger à froid, mais officiellement, en emploie le terme de Machine Hammer Peening (MHP). Un procédé relativement jeune avec lequel, dans la pratique, on peut noter d’énormes réussites (comme dans l’entreprise Aesculap AG à Tuttlingen). Ceci est rendu possible grâce à l’utilisation de l’outil de forgeage à froid FORGEfix® P.
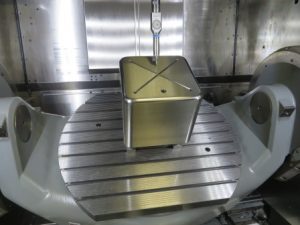
La durée totale d’usinage du tampon d’emboutissage était de 48 heures, entièrement sans personnel.
Pour l’entreprise Aesculap, il s’agissait de polir des outils d’emboutissage (tampon et matrice) à partir d’un acier chromé 1.2379 avec une dureté HRC 60 pour des containers stériles. Il y a six ans, nous avions déjà testé dans ce domaine un procédé à base électromagnétique pour lisser une surface mais, pour des raisons économiques, la réussite espérée ne fut pas au ren-dez-vous. Ainsi, jusqu’à maintenant, ces outils d’emboutissage continuaient d’être polis, ce qui coûteux en temps et en argent. Une opération qui, à Tuttlingen, n’était plus acceptable.
Développement d’une stratégie et phase de test
Pour cette raison, en collaboration avec le conseiller technique en application compétent de POKOLM, une stratégie a été développée. Celle-ci éliminait non seulement totalement le po-lissage coûteux de 60 heures mais permettait aussi d’avoir des effets annexes extrêmement positifs.
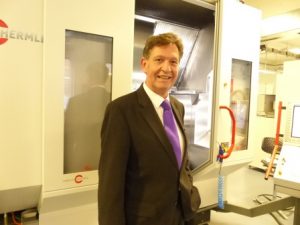
Hans Keller, directeur R + D Productions chez Aesculap AG
En font partie non seulement le lissage économique, reproductible et de grande quali-té de surfaces complexes mais aussi l’application d’une contrainte de compression et une augmentation de la dureté. Des propriétés que Hans Keller, directement R + D Productions chez Aesculap AG peut démontrer avec des chiffres concrets : « Depuis plus six ans nous traitons ce problème et, pour cette raison, nous avons testé intensément l’outil de forgeage à froid FORGEfix® P. Tout d’abord, il s’agissait de savoir quelles qualités de surface il nous permettait d’obtenir. Un résultat de Ra 0,08 m’a naturellement satisfait. D’une part il s’agit d’un lissage reproductible régulier impossible à réaliser manuellement. D’autre part, cette opération se fait chez nous entièrement sans personnel. De plus, nos mesures ont démontré une aug-mentation de la dureté de 8 %, c’est-à-dire à HRC 62. Je suis persuadé que nous aurons une prolongation mesurable des durées de vie de nos outils. »
Configurable en fonction du projet et du client
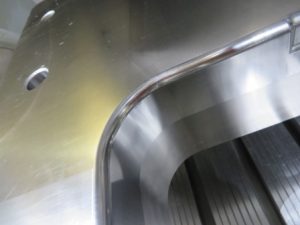
Le résultat d’une qualité de surface de Ra 0,08 est très apprécié.
Pour différentes raisons, cette phase de test intense est impérative pour l’utilisation de FORGEfix® P. D’une part, le processus doit être considéré dans sa globalité. Ceci com-mence dès la finition de la pièce. La surface doit être structurée de telle manière à ce que les pointes de rugosité puissent être fixées de manière optimale dans les creux. D’autre part, il faut que l’avance, le décalage latéral, la force de frappe ou aussi le diamètre de la bille con-viennent. Des paramètres qui dépendent essentiellement de la matière utilisée et qui, pour Sascha Leicht, technicien d’application chez POKOLM, sont absolument décisifs pour une utilisation réussie : « FORGEfix® P ne peut pas être utilisé partout et toujours. Ce qui est dé-cisif, ce sont les propriétés de la matière et quels secteurs et comment ils doivent être conso-lidés. Ici, nous sommes partenaire de développement avec le détenteur du brevet et nous proposons l’outil avec des réglages de force de 250 N, 500 N et 1.000 N ainsi que différents diamètres de bille. En fonction du projet, l’outil peut aussi, par exemple, être configuré par le répartiteur de pression intégré ou aussi en fonction de la taille du piston chez le client. »
La possibilité de configurer individuellement FORGEfix® P a conduit, chez Aesculap, à dé-couvrir d’autres applications dans la phase de test. Comme par exemple l’augmentation de la durée de vie pour les matrices de forgeage en 1.2343 ainsi que des plaquettes pour les outils composites ou la finition des implants de genoux en CoCr et en alliage au titane, sans oublier les inserts formés pour les outils de fonte par injection.
POKOLM propose le système de forgeage à froid exclusivement avec un filetage M16 côté machine.