Polishing process with positive side effects com-pletely eliminated
It is sometimes called tapping or cold forging, but officially it is known as Machine Hammer Peening (MHP). A procedure that is still relatively new, but with which major successes are already being achieved in practice, as is the case for Aesculap AG in Tuttlingen, Germany. The cold forging tool FORGEfix® P makes this possible.
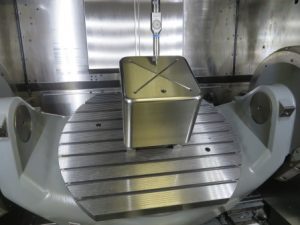
The complete drawing punch was machined in only 48 hours complete-ly unattended.
For the company Aesculap, the task in hand was the polishing of drawing tools (punch and die) from chromium steel 1.2379 with HRC 60 for sterile containers. For this area, an elec-tromagnetic procedure for smoothing the surface had already been in use six years ago, which did however not lead to the desired outcome from an economical point of view. Up to this point, these drawing tools were still polished after milling, which was time-consuming and cost-intensive. A work process which had long ceased to be acceptable in Tuttlingen.
Strategy development and test phase
For this reason, a strategy was developed together with the responsible technical application consultant of POKOLM, which not only completely eliminated the previous polishing process of 60 hours, but with which highly positive side effects could also be achieved.
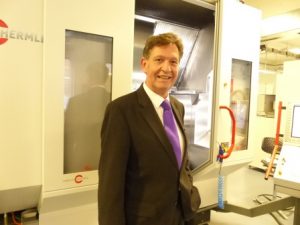
Hans Keller, R+D Productions Director at Aesculap AG
In addition to the economical, reproducible, high-grade smoothing of complex surfaces, this also included the introduction of residual compressive stress and increased hardness. Proper-ties, which Hans Keller, R+D Productions Director at Aesculap AG is able to prove with con-crete figures: “We have been looking into this issue for six years, and for this reason we have thoroughly tested the cold forging tool FORGEfix® P. First of all the question was which sur-face finish we were going to achieve. Of course I was very impressed with the result of Ra 0.08. On the one hand, it is an even reproducible smoothing which cannot be achieved in the same way manually. On the other hand, this procedure is performed unattended. Further-more, our measurements have shown an increase of hardness by 8%, i.e. HRC 62. I am ex-pecting to see a measurable extension of service life for our tools.”
Project-related and customisable
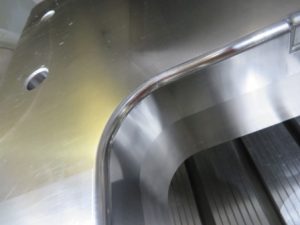
The result of a surface quality of Ra 0.08 was impressive.
This intensive test phase is essential for the use of FORGEfix® P for various reasons. Firstly, the process must be viewed as a whole. This already applies to the finishing of the workpiece. The surface must be structured so that the peaks can be optimally hardened in the valleys. Secondly, it is important to adjust the feed, lateral offset, impact force and diameter of the sphere. Parameters that mainly depend on the material used and are thus crucial for a suc-cessful application, explained Sascha Leicht, application engineer at POKOLM: “FORGEfix® P cannot always be used meaningfully for any application. The material properties are crucial, and which areas are to be hardened in which way. We are a development partner of the patent holder and offer the tool with force settings of 250 N, 500 N and 1,000 N and different sphere diameters. The tool can also be customised in accordance with the customer project by way of integrated pressure distributors or piston sizes, for example.”
The option to configure FORGEfix® P individually has meant that further applications are currently being tested at Aesculap. This includes, e.g. an increase of the service life of forging dies from 1.2343 and cutting inserts for progressive tools or the finishing of knee implants from CoCr and titanium alloy, as well as of mould inserts for injection moulding tools.
POKOLM offers the cold forging system exclusively with machine-end M16 connecting thread.