Reduce crater wear and extend service lifetime
– with solid carbide end mills up to 65 HRC
The company Fuchs Schraubenwerk GmbH, which operates from two locations in the small German city of Siegen, is the acknowledged manufacturer of a variety of sophisticated products, including high-precision formed parts, special fasteners, HV bolts and bolts for steel construction. The roots of the owner-managed company, which today employs a workforce of around 200 people, can be traced back to the early 19th century.
For some years now, the in-house tool shop has worked with a Genos M460R machining centre from Okuma, which is used to manufacture batches of stamping and forming tools in hardened high-speed steel for the production centre. The machining of this 1.3343 grade material is by no means trivial and poses particular challenges for the cutting tool.
Specific task description
Fuchs approached the responsible technical application consultant at POKOLM in search of solutions for two specific problems, namely high crater wear and the reduced service life of its solid carbide end mills. The requirement – by way of direct comparison in the machining of a specific test component – was to find a solid carbide end mill which was better able to satisfy the high demands when machining hardened high-speed steel. The chosen test component was a trimming die which is used in the manufacturing process for certain special fasteners. The cylindrical die is 35 mm high and 60 mm in diameter, and a batch of 30 pieces was to be produced. The machining task was to cut a bevel around a defined contour in the centre of the upper surface.
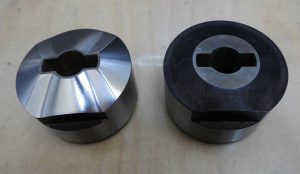
Test component before and after machining
For the practical test, two solid carbide ball-nose end mills with 2 flutes and a diameter of 4 mm were subjected to direct comparison under identical conditions. One of these end mills was the high-quality mill used by Fuchs to date, the other a POKOLM end mill with optimised geometry, carbide and coating from the new range for hard machining up to 65 HRC.
A result which could hardly be more conclusive
The new POKOLM end mill was able to machine seven parts over a service lifetime of 210 minutes. The previously used end mill, by contrast, was already in need of replacement due to heavy crater wear after just three machined parts and a service lifetime of 90 minutes.
But it was not only in terms of service life that the new POKOLM end mill emerged as the uncontested winner. It was similarly way out in front with regard to the decisive aspect of economic efficiency.
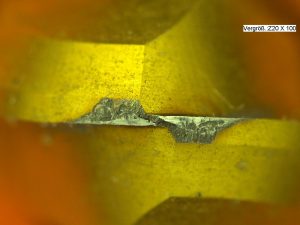
High-quality end mill from another manufacturer
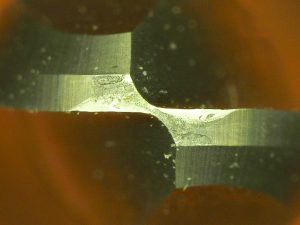
POKOLM B2HA0400321006S